HÄUFIGE FEHLER BEIM LEITERPLATTENDESIGN
KUPFER-MUSTER
Wir sehen uns häufige Leiterplattenfehler in Cad-Dateien an. Um die Herstellung von Leiterplatten effizient und zeitsparend zu gestalten, empfehlen wir die folgenden Lösungen, um diese Fehler zu vermeiden. Kupfermusterfehler sind das erste Thema in unserer Serie über häufige Designfehler.
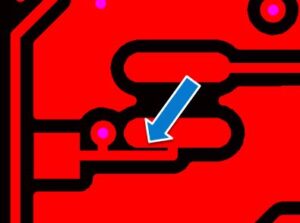
Problembeschreibung:
Probleme mit gleichen Netzabständen treten häufig dadurch auf, dass das Setup in den CAD-Systemen andere (niedrigere) Werte für gleiche Netzabstände als für die Abstände zwischen verschiedenen Netzen vorsieht. Dies kann in den gleichen Netzen zu Problemen mit zu niedrigen Isolationen führen, die zu Bandproblemen und/oder zu Lötmaskenöffnungen führen, die nahe gelegenes Kupfer freilegen.
Lösung:
Um solche Probleme zu vermeiden. Es ist ratsam, für "gleiche Netzabstände" die gleichen Einstellungen zu verwenden wie für "unterschiedliche Netzabstände".
Problembeschreibung:
Bei Platinen mit plattiertem Kupfer und wenn standardmäßig alle Löcher zusammen gebohrt werden, um die besten Lochpositionstoleranzen zu erzielen. Bei einigen Designs liegen die Kupfermerkmale zu nahe an den nicht plattierten Löchern oder die Kupfermerkmale verdecken die nicht plattierten Löcher. Bei Kupfermerkmalen, die zu nahe an nicht galvanisierten Löchern liegen, würde dies nach den Toleranzen zu beschädigten Kupfermerkmalen wie beschädigten Leiterbahnen und Lötaugen oder zu Rückständen der Kupferbeschichtung in der nicht galvanisierten Lochwand führen. Abhängig von den Produktionsprozessen in der Fabrik kann es auch unmöglich sein, ein solches Design zu produzieren, da es bei der Leiterplattenproduktion zu Rissen im Trockenfilm führen würde. Eine solche rissige Trockenfolie kann sich ablösen und zu Folienresten auf der Leiterplatte und fehlerhaften Leiterplatten führen. Oder wenn die Kupfermerkmale die nicht plattierten Löcher vollständig abdecken, würde dies dazu führen, dass die nicht plattierten Löcher zu plattierten Löchern werden.
Lösung A:
In der Leiterplattenproduktion ist es vorzuziehen, dass alle Löcher im gleichen Bohrprozess gebohrt werden, um die besten Lochpositionstoleranzen zu erreichen. Um alle Löcher gemeinsam zu bohren, die oben genannten Probleme zu vermeiden und die nicht plattierten Löcher als nicht plattiert zu erhalten , wird empfohlen, Kupfermerkmale mit einem Abstand von mindestens 250 µm von den nicht plattierten Lochrändern zu entwerfen (gilt für 35 µm Endkupferdicke). Für dickeres Kupfer gelten andere Werte (z. B. wird für 70 µm fertiges Kupfer ein Abstand von 300 µm zwischen Kupfermerkmalen und nicht plattierten Lochrändern empfohlen).
Lösung B:
Wenn die Kupfermerkmale zu nahe an den Rändern der nicht plattierten Löcher liegen oder wenn die Kupfermerkmale die nicht plattierten Löcher vollständig bedecken, gibt es eine weniger geeignete Lösung, da ein zweites Bohrverfahren für solche nicht plattierten Löcher möglich ist. Der Nachteil des zweiten Bohrverfahrens besteht jedoch darin, dass es zu freiliegendem Kupfer und eventuellen Graten an den Rändern der nicht plattierten Löcher führen kann, da die zweiten Bohrungen nach den Toleranzen in die zu nahen Kupfermerkmale einschneiden können. Außerdem können die zweitgebohrten nicht plattierten Löcher schlechtere Toleranzen als die Standard-Lochpositionen aufweisen, was ein weiterer Grund ist, diese Lösung möglichst zu vermeiden. Das freiliegende Kupfer an den Rändern der nicht plattierten Löcher kann nach dem Montageprozess beim Kunden ebenfalls zu einem Engpass führen. (Zum Beispiel, wenn dasselbe nicht-plattierte Loch freiliegendes Kupfer auf mehreren Kupferlagen mit unterschiedlichen Netzen verursacht). Wenn also diese Lösung B verwendet wird, muss der Kunde auch sicher sein, dass kein Risiko für ein mögliches Mangelproblem besteht.
Problembeschreibung:
Ein Kupfermerkmal eines Netzes liegt zu nahe an den Kanten eines anderen Netzes, das mit Löchern plattiert ist - dies kann zu einem Engpass zwischen verschiedenen Netzen führen.
Lösung:
Es wird empfohlen, einen Abstand von mindestens 300µm zwischen den Netzkupfermerkmalen und den Lochkanten eines anderen netplattierten Bauteils einzuhalten (mindestens 250µm von den Kanten der Standard-Via-Löcher), um das Risiko von Engpässen zu vermeiden. Natürlich ist ein größerer Abstand noch besser (gilt für 35µm Endkupferdicke). Für dickeres Kupfer werden andere Werte angewandt. (Beispiel: bei 70µm fertigem Kupfer wird ein Abstand von mindestens 350µm von einer Netzkupfermerkmalskante zu einer anderen Netzplattierungskomponenten-Lochkante empfohlen). (mindestens 300µm von Standard-Durchgangslochkanten). Natürlich ist ein größerer Abstand noch besser.
Problembeschreibung:
Eine solche Konstruktion kann zu ungleichmäßigen Kupferschichtdicken führen. Und auf Schichten mit Kupferbeschichtung, wo die "bow & twist" dann nicht den empfohlenen Standard erfüllen kann.
Lösung:
Um solche Probleme zu vermeiden, sollte das Kupfer so gleichmäßig wie möglich auf derselben Schicht verteilt sein. Und auch so symmetrisch/ausgeglichen wie möglich zwischen verschiedenen Kupferschichten.
Problembeschreibung:
Zu kleine "Flutungsabstände" zu den meisten Teilen der Muster machen die Produktion schwieriger als sie sein müsste. Das kann sich dann auf den Preis auswirken.
Lösung:
In den meisten Fällen gibt es keinen Grund für einen zu geringen "Flutungsabstand". Ein guter Wert ist ein Wert von 150-250µm zwischen der Flutung und den Plattenmerkmalen.
Beschreibung des Problems:
Die Kupferabstände sind zum Platinenumriss hin zu gering. (und/oder in Richtung der nicht plattierten Steckplätze). Dies kann zu freiliegendem Kupfer und Graten entlang der Platinenumrandung (oder entlang der nicht plattierten Schlitze) führen. Eventuell abweichendes, freiliegendes Kupfer an den Leiterplattenkanten oder nicht beschichteten Schlitzen kann auch nach dem Montageprozess beim Kunden zu Engpässen führen. (Zum Beispiel, wenn freiliegendes Kupfer auf mehreren Kupferlagen mit unterschiedlichen Netzen liegt). In vielen Fällen müssen die Designer auch berücksichtigen, dass der Bestückungsprozess oft eine Art von Array mit V-Schnitt (Scoring) oder Routing mit Break Tabs erfordert. Es ist daher sinnvoll, das Design für diesen Fall zu planen und Platz für Bruchkanten und/oder V-Cuts vorzusehen.
Lösung:
Zur Vermeidung von Graten und freiliegendem Kupfer an den Konturen (und an nicht plattierten Schlitzen). Eine gute Regel für das Design ist es, Kupfermerkmale mindestens 0,25 mm von den gefrästen Konturen und von nicht plattierten Schlitzkanten entfernt zu halten. (Gilt für eine endgültige Kupferdicke von 35µm). Für dickeres Kupfer gelten andere (höhere) Werte. Wenn die Konturen gefräst werden, dann sollten Sie auch geeignete kupferfreie Bereiche entlang der Konturen für Sollbruchstellen (und für Sollbruchstellenlöcher) vorsehen. An solchen Stellen kupfern Sie mindestens 0,7mm von den Konturen ab und die kupferfreien Bereiche etwa mit 5mm Länge. Beim V-Schnitt muss der Abstand zwischen Kupfer und V-Schnitt-Konturen mindestens 0,45 mm betragen (gilt für 35 µm Endkupferdicke). Für dickeres Kupfer gelten andere (mehr) Werte. Bitte beachten Sie auch, dass bei V-Cut-Platten, die dicker als 1,6mm sind, der Abstand zwischen Kupfer und Kontur weiter vergrößert werden muss.
Beschreibung des Problems:
Zu kleine Texte/Zahlen in Kupfer - kann zu unklaren Texten auf den fertigen Leiterplatten führen. Probleme bei der Leiterplattenproduktion, da zu kleine Texte/Zahlen oft Teile mit sehr kleinen Isolierungen (kleine Splitter im Kupfer) haben, die sich bei der Produktion ablösen können, was zu Kurzschlüssen, offenen Stellen und Lötbarkeitsproblemen führt.
Lösung A:
Als erste Wahl wird empfohlen, alle Texte/Ziffern nur im Siebdruckverfahren zu gestalten. Die empfohlene Textzeilenbreite beträgt 0,13 mm oder mehr und die Texthöhe mindestens 0,8 mm. Der Siebdruck sollte so gestaltet werden, dass offene Bereiche der Lötmaske und Löcher vermieden werden. Verwenden Sie nur notwendige Zahlen (Text) in Kupfer (z.B. Lagennummern) und dann natürlich in der richtigen Größe (siehe andere Lösung.
Lösung B:
Um solche Textprobleme zu vermeiden und wenn die andere Lösung (Siebdruck) nicht möglich ist, wird empfohlen, eine Kupferlinienbreite von 0,2 mm oder mehr mit einer Text-/Zahlenhöhe von 2 mm oder mehr zu verwenden (größer ist besser). Wichtig ist auch, dass zwischen den Kupfertextzeilen genügend Abstand bleibt.