ERROS COMUNS EM DESIGN
PADRÃO DE COBRE
Analisamos os erros comuns no desenvolvimento de placas de circuito impresso nos ficheiros Cad. Para tornar a fabricação de PCIs eficiente e poupar tempo, recomendamos as soluções abaixo para evitar estes erros. Os erros de padrão de cobre são o primeiro tópico da nossa série de erros de design comuns.
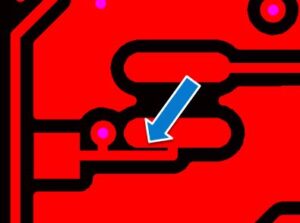
Descrição do problema:
As dificuldades de espaçamento da mesma trilha são normalmente observadas pelo fato de que a configuração nos sistemas CAD pode ter valores diferentes (mais baixos) para o espaçamento da mesma trilha do que o espaçamento entre trilhas diferentes. Isto pode causar problemas nas mesmas trilhas com isolamentos muito baixos nas mesmas trilhas, o que resulta em problemas de fitas e/ou em aberturas na máscara de solda que expõem o cobre próximo.
Solução:
Para evitar estes problemas. Pode ser aconselhável utilizar as mesmas definições para "o mesmo espaçamento de trilha" e para "espaçamento de trilha diferente".
Descrição do problema:
Nas placas com cobre revestido e se como padrão, todos os furos são perfurados juntos para obter as melhores tolerâncias de posição dos furos. Em alguns projetos, os elementos de cobre estão muito próximos a orifícios não revestidos ou os elementos de cobre cobrem orifícios não revestidos. Se os elementos de cobre estiverem muito próximos dos orifícios não revestidos, após as tolerâncias, os elementos de cobre ficarão danificados, como traços e almofadas danificados, ou poderão resultar em resíduos de revestimento de cobre na parede do orifício não revestido. Além disso, dependendo dos processos de produção da fábrica, pode ser impossível produzir um desenho deste tipo, uma vez que provocaria fissuras na película seca na produção da PCI. E essa película seca fissurada pode descolar-se, causando resíduos de película na placa e placas defeituosas. Ou se os elementos de cobre cobrirem totalmente os orifícios não galvanizados, isso fará com que os orifícios não galvanizados se transformem em orifícios galvanizados.
Solução A:
Na produção de PCIs, é preferível que todos os furos sejam efetuados em conjunto no mesmo processo de perfuração para obter as melhores tolerâncias de posição dos furos, pelo que, para perfurar todos os furos em conjunto e evitar os problemas acima referidos e para manter os furos não revestidos como não revestidos, recomenda-se que as características de cobre sejam concebidas a uma distância mínima de 250µm das bordas dos furos não revestidos (aplica-se a uma espessura final de cobre de 35µm). Para cobre mais espesso, aplicam-se outros valores (por exemplo, para cobre acabado de 70µm, recomenda-se uma distância de 300µm entre os elementos de cobre e as bordas dos furos não revestidos ).
Solução B:
Se os elementos de cobre estiverem muito próximos das bordas dos furos não revestidos ou se os elementos de cobre cobrirem totalmente os furos não revestidos, existe uma solução menos adequada, uma vez que é possível efetuar um segundo processo de perfuração para esses furos não revestidos. No entanto, a desvantagem do segundo processo de perfuração é que pode resultar em cobre exposto e eventuais rebarbas nas bordas dos furos não chapeados, uma vez que, após as tolerâncias, os segundos furos podem cortar os elementos de cobre muito próximos. Além disso, a segunda perfuração de furos não revestidos pode resultar em tolerâncias de posição de furos piores do que o padrão, o que é outra razão, se possível, para evitar esta solução. O cobre exposto nas bordas dos orifícios não galvanizados pode também causar uma escassez após o processo de montagem pelo cliente. (Por exemplo, se o mesmo orifício não revestido causar cobre exposto em várias camadas de cobre com trilhas diferentes). Assim, se esta solução B for utilizada, o cliente também deve certificar-se de que não existe o risco de um eventual problema de escassez.
Descrição do problema:
Um elemento de cobre de uma trilha muito próxima das bordas dos orifícios chapeados de outra trilha - pode causar uma falta entre trilhas diferentes.
Solução:
Recomenda-se que se mantenha uma distância de pelo menos 300µm entre as bordas dos orifícios de uma trilha de cobre e as bordas dos orifícios de outra trilha de componentes revestidos (pelo menos 250µm das bordas dos orifícios da via padrão) para evitar o risco de escassez. Naturalmente, uma distância maior é ainda melhor (aplica-se a uma espessura final de cobre de 35µm). Para cobre mais espesso, são aplicados outros valores. (Exemplo: se a espessura final do cobre for de 70µm, recomenda-se uma distância mínima de 350µm entre um bordo de cobre e outra borda de orifício de componente revestido). (pelo menos 300µm dos bordos dos orifícios da via standard). Naturalmente, uma distância maior é ainda melhor.
Descrição do problema:
Esta concepção pode provocar espessuras de revestimento de cobre desiguais. E em camadas com revestimento de cobre onde o "arco e torção" não pode então cumprir a norma recomendada.
Solução:
Para evitar estes problemas, o cobre deve ser distribuído o mais uniformemente possível na mesma camada e tão simétrico/equilibrado quanto possível entre as diferentes camadas de cobre.
Descrição do problema:
Um "espaçamento de muito pequeno para a maioria das partes dos padrões torna a produção mais difícil do que é necessário. Isto pode afetar o preço.
Solução:
Na maioria dos casos, não há razão para ter um "espaçamento de inundação" muito pequeno. Assim, um bom valor é utilizar um valor de 150-250µm entre a inundação e as características da placa.
Descrição do problema:
O espaçamento do cobre é muito pequeno em relação ao contorno da placa. (e/ou em direção às ranhuras não revestidas), podendo causar cobre exposto e rebarbas ao longo do contorno da placa (ou ao longo das ranhuras não revestidas). Eventualmente, a existência de cobre exposto nas bordas da placa ou nas ranhuras não galvanizadas pode também causar escassez após o processo de montagem pelo cliente. (Por exemplo, se houver cobre exposto em várias camadas de cobre com trilhas diferentes). Além disso, em muitos casos, os projetistas têm de ter em consideração que o processo de montagem necessita frequentemente de algum tipo de matriz com corte em V (pontuação) ou encaminhamento com separadores de rutura. Por conseguinte, é bom planear o projeto para este efeito e criar espaço para separadores de rutura e/ou corte em V.
Solução:
Para evitar rebarbas e cobre exposto nos contornos (e nas ranhuras não revestidas). Uma boa regra para o projeto é manter as características do cobre a pelo menos 0,25mm dos contornos roteados e das bordas das ranhuras não chapeadas. (Aplica-se a uma espessura final de cobre de 35µm). Para cobre mais espesso, são aplicados outros (mais) valores. Se os contornos forem fresados, considere também a possibilidade de ter áreas livres de cobre adequadas juntamente com os contornos para os separadores de rutura (e para os orifícios dos separadores de rutura). Nesses locais, cobre pelo menos 0,7 mm dos contornos e as áreas livres de cobre com comprimentos de aproximadamente 5 mm. Para o corte em V, manter pelo menos uma distância de 0,45mm entre o cobre e os contornos do corte em V (aplica-se a uma espessura final de cobre de 35µm). Para cobre mais espesso, são aplicados outros (mais) valores. Tenha também em atenção que, para placas com corte em V com espessura superior a 1,6 mm, a distância entre o cobre e o contorno tem de ser aumentada.
Descrição do problema:
Valores de cobre muito pequenos podem resultar em trilhas pouco claras nas placas acabadas. Uma vez que são utilizados valores muito pequenos têm frequentemente peças com isolamentos muito pequenos (pequenas lascas no cobre) que podem descolar-se na produção, dando origem a curtos-circuitos, aberturas e problemas de soldabilidade.
Solução A:
Como primeira opção, recomenda-se a conceção de todos os textos/números apenas em camada(s) de serigrafia. A largura recomendada da linha de texto é de 0,13 mm ou mais e a altura do texto é de, pelo menos, 0,8 mm. A serigrafia deve ser concebida de modo a evitar áreas abertas da máscara de soldadura e a evitar buracos. Utilizar apenas os números (texto) necessários em cobre (por exemplo, números de camadas) e, naturalmente, com as dimensões corretas (ver outra solução).
Solução B:
Para evitar tais problemas de texto e se a outra solução (serigrafia) não for possível, recomenda-se a utilização de uma largura de linha de cobre de 0,2 mm ou mais com uma altura de texto/número de 2 mm ou mais (quanto maior, melhor). É igualmente importante manter um espaço suficiente entre as linhas de texto em cobre.